To be a good leader, safety should already be part of your leadership toolkit, not an ‘add-on’
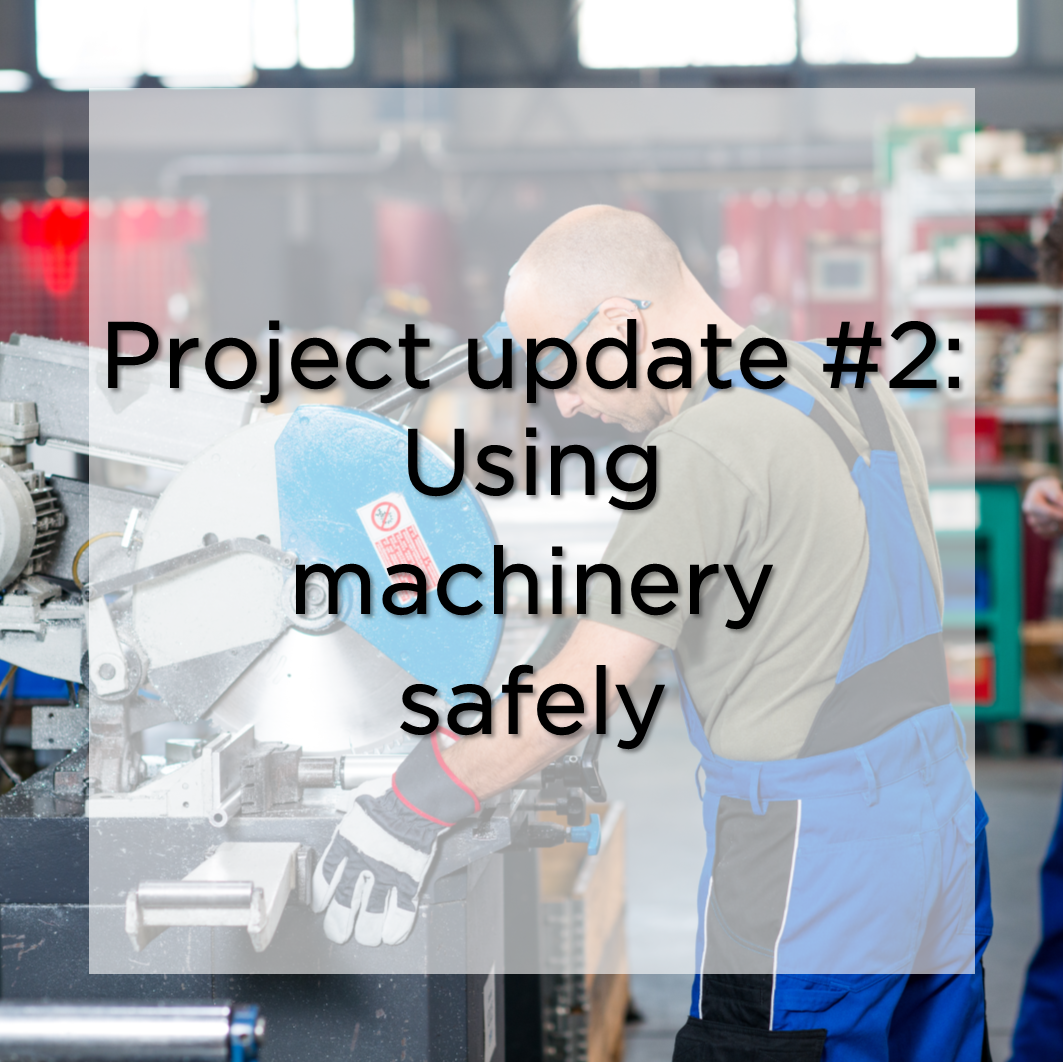
Safety leadership can mean different things to different people. To some, it is about putting safety first during decision making. Others describe safety leadership as caring about others’ health and safety at work. It can even be about following best practice in your industry and inspiring others to do the same.
Yet, when it boils down to it, safety leadership is essentially general leadership applied to safety situations.
Research has shown that ‘good’ leadership in the context of safety is driven by four different sets of behaviours:
- Transactional: Setting minimum standards for safety, recognising good safety performance and correcting problems before they cause harm.
- Transformational: Inspiring others to take on safety goals as their own, through role modelling, positive influence and challenging people to come up with solutions.
- Authentic: Being open to feedback and having a willingness to admit mistakes.
- Empowering: Sharing safety decision making, advocating or standing up for workers’ rights.
The reason why ‘safety leadership’ can be unhelpful as a concept is because it suggests that a leader adopts a special style just for safety. This treats safety as an ‘add-on’ to ordinary leadership. In other words, that safety is something extra or different that a leader is doing.
More helpful is to talk about good general leadership, combined with a priority and commitment to safety. This approach treats safety as an integrated and central part of good leadership.
In fact, our interviews with 60 workers, supervisors, managers and safety inspectors revealed a number of ‘safety leadership’ behaviours that are just good general leadership. These behaviours include:
- Educating workers on the benefits of working safely with machines.
- Verifying that machine operators are adhering to safe standards of work.
- Explaining the reasons why operators need to adhere to machine safety requirements.
- Encouraging machine operators to share their views on how machine safety should be achieved.
- Talking about safety during team meetings.
- Asking machine operators for their input into safety procedures.
- Gathering operators together to talk about machine safety.
- Walking around the shop floor observing machine operators' safety.
- Interacting with machine operators and listen to their concerns about safety.
- Participating in workplace safety activities and initiatives (e.g. committee meetings).
- Taking the time to develop a positive working relationship with machine operators.
- Making it known that machine operators can stop or refuse the job if it is unsafe.
- Encouraging machine operators to suggest what to do about a safety issue.
We’d like to thank the following businesses for participating in the research: Access Industries, Faircloth Reynolds, Hi Con Services Pty Ltd, ACT Steelworks, Rockpress, WDT (Engineers) Pty Ltd, Reliance Hexham Pty Ltd, Sell & Parker, Precision Oxycut, AllThread Industries, TREW Enterprises Pty Ltd, Frucor Suntory.